An interview about the extensive quality control tests ZEISS thermal imaging cameras undergo and why the laboratory has to be relocated to the forest from time to time.
The next part of our series of articles on the development of the ZEISS DTI 3 thermal imaging camera family looks at the process of validating the prototypes. In previous interviews, we already gained exciting glimpses behind the scenes and into the work of Category Management and System Engineering. The team from System Engineering explained the process of creating a prototype in the predevelopment and main development stages and presented an initial impression of the associated demanding tests to put the prototypes through their paces. Today we are going to take a closer look at this process in an interview with Stefan Reiser (Senior Scientist, Laboratory & Application Testing) and find out what kinds of stress the DTI had to withstand over the course of its development, as well as learn what made him become a passionate hunter in the first place.
In previous articles, we have learned about the important development stages and the people behind product development.
To ensure that a product ultimately meets ZEISS’ demanding standards of quality, however, it must be able to withstand extensive testing. This is where you come in, Stefan. Please briefly explain what your work looks like when it comes to validating the prototypes.
Stefan: “Essentially, our work can be divided into two stages: our lab tests here in-house and, of course, our hands-on use in the field – literally. In this process, we are responsible for identifying all of the potential hazards or stresses that our products must withstand in everyday use and for testing our prototypes in this regard in close coordination with Category Management and System Engineering. Together, we consider where we can add technical features or, for example, more robust materials. It goes without saying that our work also includes an examination of competitor’s products.“
You just mentioned that your team divides testing into lab testing and field testing. What kinds of things did you test when it came to the DTI 3 family, and what did it have to withstand?
Stefan: “A large part of our testing relates to the environmental impact and durability of the products throughout their lifetime. In our tests, we try to simulate future stress that would occur over a period of many years within a few days and weeks. For example, we expose the DTI to particularly high and freezing cold temperatures as well as shock loads that occur during transport and use. We test the surfaces to see how they react to substances such as gun oil or body cream. Does residue build up on the surface, especially on the rubberized parts of the DTI, or can users easily clean the device? Does the material become brittle, or does it change its properties due to these stresses?”
During many years of use, the DTI is exposed to numerous unavoidable factors, such as UV radiation, water, salt spray, or dust. We also simulate these external effects in the laboratory. In doing so, we base our testing on the specifications of the relevant ISO standards. This allows us to ensure that the DTI meets the specifications of the IP66 rating, for example, this means that the DTI’s electronic components are fully protected against the penetration of dust and powerful water jets.
For this dust test, for example, the DTI is connected to a vacuum and exposed to fine dust or talcum powder swirling around the test chamber for hours. In the water jet test, on the other hand, the device is placed on a rotating plate and then blasted with a powerful jet of water from all sides. In this demonstration you could say, that we recreate an entire product life cycle in our laboratory in an reduced time frame! If our products ever fail to withstand the tests, it’s back to the drawing board to make the necessary changes to the material or to the details of the design.”
During the dust test, the DTI is connected to a vacuum to expose it to fine talcum powder for several hours (IP6x).
During the water jet test, the DTI is blasted with powerful streams of water from all sides (IPx6).
In addition to these external factors, the product’s inner values also play a key role, of course! What testing methods do you use for this purpose?
Stefan: “Our testing doesn’t just cover environmental factors. Image quality and image processing are both of central importance. We also initially conduct laboratory tests for this purpose. After all, our highly sophisticated optics are one of the flagship features of our ZEISS DTI. To this end, we develop our own measurement technology for some of our products in order to assess and improve edge and detail sharpness as well as symmetry using various test models.
When it comes to the interaction between the eyepiece and the display, we also examine whether reflections, i.e., ghost images, appear or whether we can detect too much stray light.
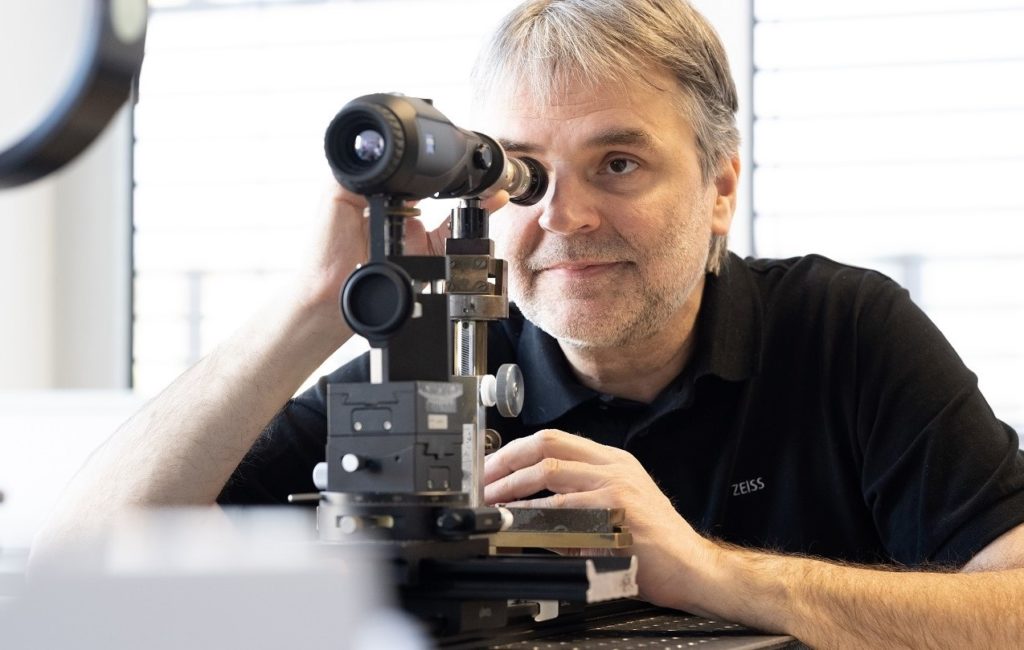
MTF measurement is one of the methods used to test the thermal imaging lens. MTF stands for modulation transfer function (for more information, see Part 1 | Part 2). In simple terms, the reproduction quality of the lens is “compared” with that of a physically ideal image.”
“We do not only assess optical quality in the laboratory during daylight, however – the key practical test takes place during real-life applications to verify the measured laboratory results. The actual application, i.e., use during hunting, takes place in the forest, on a raised hide, or while stalking at dusk until deep into the night. This is exactly where the DTI has to prove itself. In this process, my own visual assessment as a hunter with a great deal of experience plays a key role. In the laboratory, we can only assess the impact of climatic aspects on image quality, such as humidity, to a limited extent. At the edge of the forest and in meadows, on the other hand, we can repeat our tests on several days under different weather conditions and compare the results. Some image artifacts, for example, are only visible at night during real-world use. The new “Contrast Boost” feature that we have added via a firmware update, that makes it possible to enhance the contrast in high humidity, is also something that we can really only test in the field.
With our findings from these numerous tests, we coordinate with our colleagues from Category Management, Development, and System Engineering to clarify which adjustments may still need to be made. After all, in the end the goal is to create a ZEISS product that can withstand all of the criteria and stresses!”
You‘ve been a hunter yourself for several years – what effect does this have on your work?
Stefan: “This has made me intimately familiar with the subject matter and what our customers require. The fact that we not only conduct our work only in the laboratory, but also in the middle of the forest at twilight, in misty clearings, and in damp meadows, demonstrates the high standards of quality we set for ourselves and the precision and practical focus we apply to test them.
As a hunter myself, this is particularly gratifying for me, and I’m happy when the DTI gives me that exciting, clear view of deer grazing in the hunting grounds.”
In the final part of the series, we look at ZEISS’ customer service and why it plays an important role both during and after development.