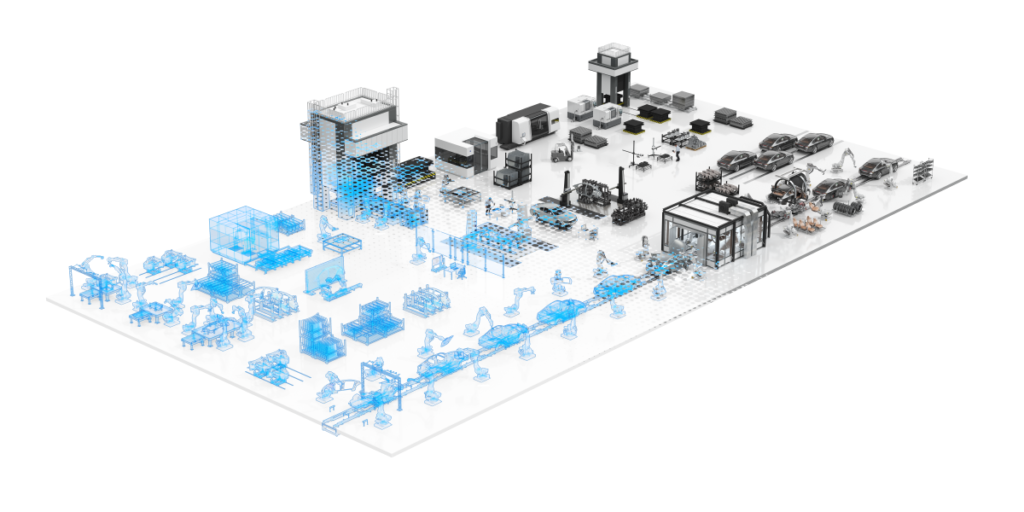
Ab den 1970er Jahren hielten Computer und Automatisierungstechnik Einzug in die Produktion. Flexible Massenproduktion war nun abseits von Fließbändern möglich. Maschinen wurden hinsichtlich maximalem Werkstückdurchsatz optimiert. Dieser bis in die 2000er Jahre anhaltende Prozess wird allgemein als dritte industrielle Revolution bezeichnet.
Die nun in den 2010er Jahren u.a. von der Bundesregierung postulierte „Industrie 4.0“ hat andere Ziele. Da die Produktivzeiten von Maschinen und ganzen Produktionstrecken in vielen Branchen weitestgehend optimiert sind, nimmt man sich nun der Optimierung von unproduktiven Zeiten an. Unproduktive Zeiten bestehen im Wesentlichen aus den Zuständen Maschinenstillstand und Ausschussproduktion.
Zwei wesentliche Ansätze zur Optimierung der unproduktiven Zeiten
Streben nach einer 100% Auslastung aller Maschinen
Erfüllen meine Produktionsmaschinen gerade nicht die Aufgabe, für die sie eingekauft und installiert worden sind, sind sie unproduktiv und erwirtschaften keinen Mehrwert. Man unterscheidet in geplanten und ungeplanten Stillstand. Einem geplanten Stillstand wird entgegengewirkt, indem man die Maschine flexibel an mehreren Stellen in der Produktionskette einsetzt. So wird insgesamt eine höhere Auslastung erreicht. Ein gut vorstellbares Beispiel ist ein 6-Achs Roboter mit einem Greifer, den man flexibel von einem Arbeitsplatz zum nächsten bringen kann, je nachdem, wo gerade Arbeit zu verrichten ist. Bei diesem Konzept spricht man von Wandelbarkeit der Produktion. Ungeplante Stillstände gehen meist auf Komponenten- und Baugruppenausfälle innerhalb einer Maschine zurück. Hier gilt es, die Wartung von Maschinen so zu organisieren, dass nur innerhalb von geplanten Zeiträumen Wartungen durchgeführt werden (vorausschauende Wartung).
Reduzierung des Ausschusses
Ein zweiter großer Ansatzpunkt ist die Reduzierung des Ausschusses. Dabei unterstützt die Prozesskontrolle, die nach jedem Arbeitsgang oder schon während eines Arbeitsganges erfolgen sollte. Aufbauend auf die Prozesskontrolle ist die Prozessregelung. Dabei werden Erkenntnisse aus der Prozesskontrolle zurück in den Arbeitsgang (Prozess) geführt und somit das Ergebnis der nächsten Durchführung des Arbeitsganges verbessert. Bei einem einzelnen Arbeitsgang kann man sich dieses Vorgehen noch sehr gut vorstellen: z.B. wird nach dem Fräsen einer Kreiskontur der Durchmesser des Kreises gemessen, bewertet und bei Abweichungen entsprechend das Fräsprogramm für das nächste Teil angepasst. Komplexere Ansätze verfolgen das Ziel, eine Prozesskontrolle über mehrere Arbeitsschritte oder sogar über Arbeitsschritte verteilt auf mehrere Unterlieferanten zu steuern.
Daten als Schlüssel zur besseren Planung
Beide Ansätze zur Produktionsoptimierung werden zum großen Teil über eine bessere Planung und Kontrolle von Prozessen beeinflusst. Bessere Planung bedingt einen deutlich größeren Pool an verschiedensten Daten, die gezielt ausgewertet werden müssen. Dabei übersteigen die Anzahl und Detaillierung der Daten die Auffassungsgabe von Menschen deutlich. Es werden komplexe Softwarelösungen gebraucht, um einen Nutzen (Mehrwert) aus diesen Daten zu erzeugen.
Je nach Reifegrad der Daten und Reifegrad der Auswertungen werden die Entscheidungen, die ein Mensch in einem Produktionsumfeld treffen muss, mehr und mehr durch Software unterstützt, bis hin zur völligen Autonomie der Produktion. Um den aktuellen Zustand der eigenen Produktion zu reflektieren, hilft das in Abbildung 1 dargestellte Data Analytics Maturity Model. Es zeigt eine Übersicht zum Zusammenhang zwischen Reifegrad der Daten und den möglichen Auswirkungen von Software auf den Entscheidungsprozess.
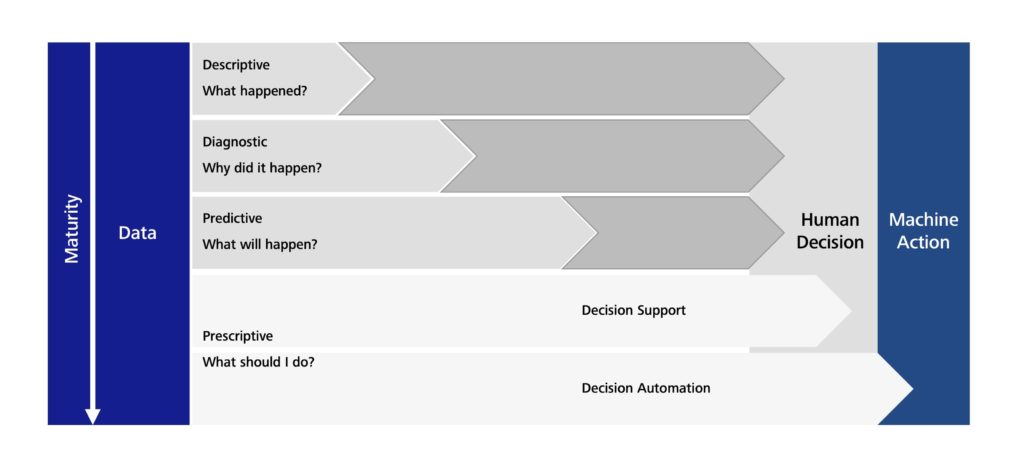
In der niedrigsten Stufe des Modells (Descriptive) geben die Daten nur Auskunft über die in der Vergangenheit liegenden Ereignisse einer Maschine oder einer Produktionstrecke. Es benötigt viel menschliche Interaktion, Diagnose und zuletzt eine menschliche Entscheidung, um die geeignete Maschinenaktion auszulösen und umzusetzen. Je reifer die Daten sind (Diagnostic und Predictive Stufe), umso weniger menschliche Interaktion ist notwendig. In der höchsten angestrebten Stufe (Prescriptive) ist es möglich, dass Software völlig autonom alle Produktionsvorgänge plant und umsetzt.
Aspekte von Daten eines digitalen Zwillings
Die Erhebung von Daten jeglicher Art führt schnell zur Problematik der Sortierung und Ordnung. Stellen wir uns ein einfaches Bauteil bzw. eine Komponente vor, wie in Abbildung 2 dargestellt. Während des Betriebes dieses Bauteils innerhalb einer Produktionsmaschine fallen zyklische Live -Daten an. In anderen Lebensphasen, z.B. während der Herstellung dieses Bauteils, sind Daten wie Stückliste und technische Zeichnungen interessanter. Möchte man Daten erheben, ohne auf das Vorhandensein des Bauteils angewiesen zu sein, bietet sich das 3D Modell und ein funktionierendes Verhaltensmodell an, mit dem man Zustände und Funktionen simulieren kann.
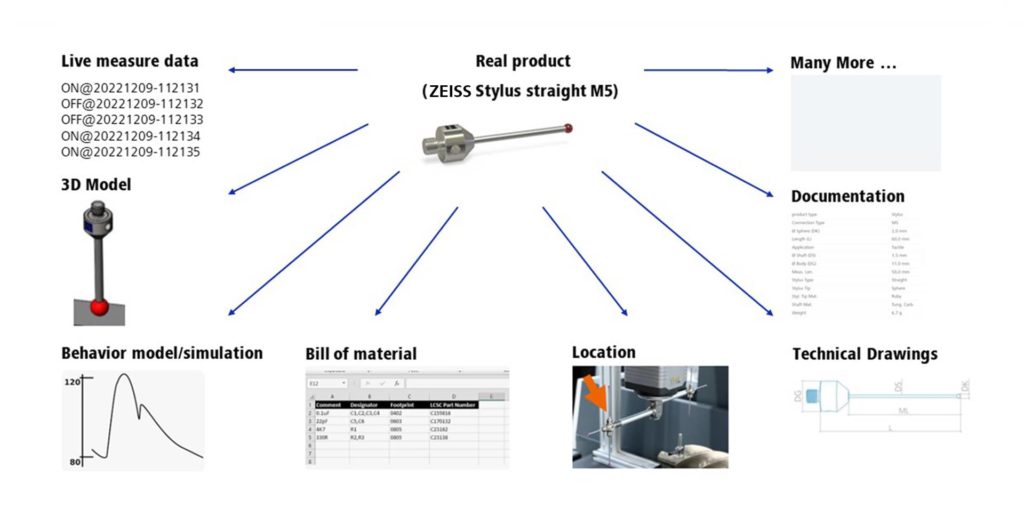
Die meisten Menschen denken bei dem Schlagwort Digitaler Zwilling zunächst nur an ein 3D Modell, welches mit Verhaltensdaten angereichert wurde und für Simulationen verwendet werden kann. Im Kontext von Industrie 4.0 ist das allerdings nur ein Aspekt unter vielen.
Die Initiative Plattform Industrie 4.0 hat folgende Definition für einen digitalen Zwilling gewählt:
Ein digitaler Zwilling ist eine digitale Repräsentation eines Produktes*, die ausreicht, um die Anforderungen einer Menge von Anwendungsfällen zu erfüllen.
Mit dieser Definition ist ein digitaler Zwilling schon geschaffen, wenn der Aspekt meines konkreten Anwendungsfalles abgedeckt wurde. Je nach Sicht und Anwendungsfall wird es also sehr verschiedene Ausprägungen von digitalen Zwillingen geben. Wichtig ist nur, dass man sich mit seinem Gesprächspartner vorher verständigt, unter welchen Aspekten man über einen digitalen Zwilling spricht.
Digitaler Zwilling: Typ und Instanz
Um weiter ein besseres Verständnis um den Digitalen Zwilling zu erlangen, unterscheiden wir in die zwei Zustände Typ und Instanz:
Typ eines digitalen Zwillings: Beschreibt alle generischen Eigenschaften aller Produkt-Instanzen. In der Softwareentwicklung ähnelt es am ehesten einer Klasse. Am häufigsten nutzt man Digitale Zwillingstypen in den Lebensphasen vor der Herstellung des Produktes, also z.B. in der Engineering Phase. Digitale Zwillingstypen werden häufig mit einer Testumgebung verknüpft, in der man versucht Eigenschaften des digitalen Zwillings zu optimieren um dann später auch das reale Produkt verbessert herzustellen.
Instanz eines digitalen Zwillings: Beschreibt den digitalen Zwilling von genau einem konkreten Produkt und ist eindeutig mit ihm verbunden. Die digitale Zwillingsinstanz existiert nur einmalig weltweit. Allerdings ist es durchaus möglich, dass eine Instanz eines digitalen Zwillings nur einen bestimmten Aspekt des konkreten Produktes abbildet. Somit können mehrere digitale Zwillinge im Kontext unterschiedlicher Aspekte nebeneinander existieren. In der Softwareentwicklung entspräche es am ehestem einem Objekt. Digitale Zwillingsinstanzen verwendet man am häufigsten im Zusammenhang mit dem Betrieb eines konkreten Produktes. Oft werden digitale Zwillingsinstanzen von Typen abgeleitet (analog der Softwareentwicklung, wo Objekte von Klassen abgeleitet werden).
Digitaler Zwilling im Herstellungsprozess
Im Kontext von Industrie 4.0 und somit im Kontext eines Herstellungsprozesses sollte man sich stets dazu verständigen, ob man bei einem Digitalen Zwilling über die Produktionsmaschine oder über das Werkstück (Produkt) spricht, um Missverständnissen vorzubeugen. Beides kann einen Digitalen Zwilling besitzen, deren Anwendungsfälle sind aber sehr verschieden.
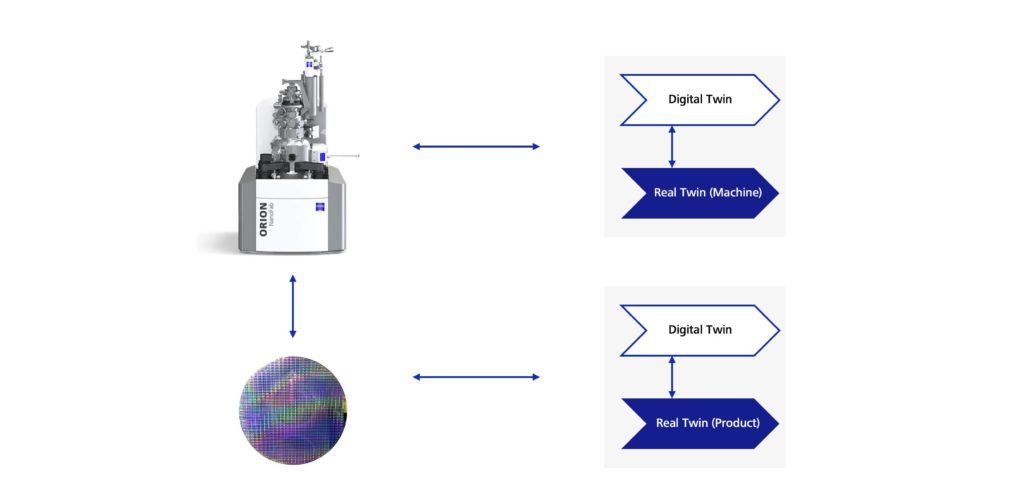
Steht die Planung der eigenen Produktion im Vordergrund meiner Überlegungen, werde ich mich wahrscheinlich mehr mit den digitalen Zwillingen meiner Produktionsmaschinen beschäftigen. Liegt mein Fokus auf der Anreicherung von Daten für meine Werkstück, und damit für mein Produkt, steht der Digitale Zwilling von eben jenem im Vordergrund. Es gibt keine klare Nutzungstrennung. Beide Betrachtungsweisen können sowohl für mich und meine Produktion genutzt werden als auch nützlich für den Nutzer meiner Produkte sein.
Einordnung digitaler Zwillinge nach dem Informationsfluss
Für eine weitere Unterscheidung in der Evolution vom digitalen Modell zum digitalen Zwilling gibt es Charakterisierungen nach dem Informationsfluss vom realen Objekt zum digitalen Objekt[2].
Digitale Modelle von Objekten sind heute schon Industriestandard. Ein prägnantes Beispiel ist das 3D Modell eines Bauteils. Es wird manuell mit Informationen angereichert (z.B. mit einem 3D CAD Programm) und man schaut sich manuell interessante Aspekte an (z.B. eine Kollisionsprüfung mit anderen 3D Modellen). Wird ein digitales Modell im Produktionsprozess zyklisch und automatisch mit Daten angereichert, spricht man von einem digitalen Schatten. Ein einfaches Beispiel wäre ein Betriebsstundenzähler eines Objektes, der automatisch durch das reale Objekt getriggert und im digitalen Objekt gespeichert wird. Auswertungen würden weiterhin manuell geschehen. Hin und wieder wird auch der Begriff digitaler Fußabdruck analog zu Digitaler Schatten verwendet. Gibt ein digitaler Schatten nun automatisch Informationen an das reale Objekt zurück und beeinflusst dessen Funktion, spricht man von einem digitalen Zwilling. Im Kontext der Plattform Industrie 4.0 spricht man weiterhin von einem cyber physischen System. Es ist Definition des Digitalen Zwillings und Realen Zwillings, welche über Datenströme miteinander verknüpft sind und sich gegenseitig beeinflussen.
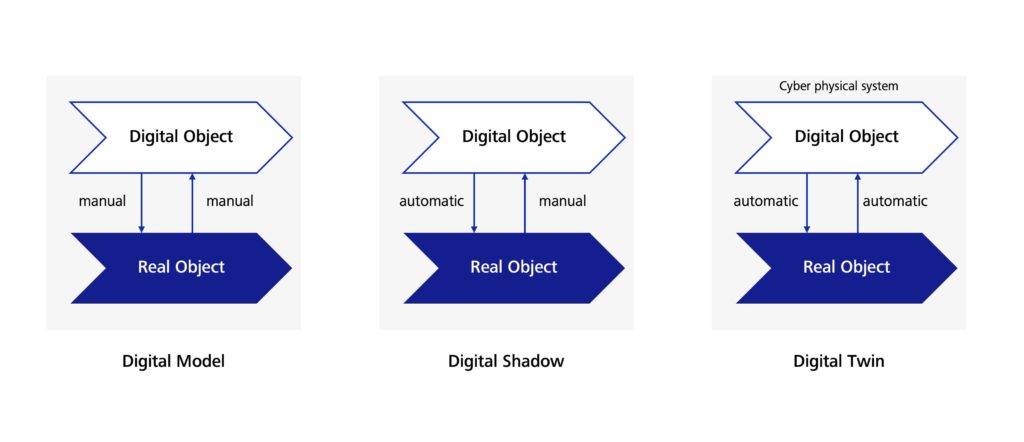
Die Einordnung nach dem Informationsfluss ist nur für Instanzen des digitalen Zwillings hilfreich. Für Typen von digitalen Zwillingen wird diese Einordnung nicht verwendet, weil das reale Objekt schlichtweg nicht existiert. Sind mehrere Aspekte innerhalb eines digitalen Zwillings zusammengefasst, sollte diese Art der Betrachtung für jeden Aspekt separat erfolgen, da unterschiedliche Aspekte in verschiedene Definitionen fallen können.
Vom digitalen Zwilling zur besseren Produktionsplanung
Die bis hier eingeführten Definitionen und Kategorisierungen sollten ausreichen, eine gemeinsame Sprache für die Beschreibung von Digitalen Zwillingen zu verwenden. Eine allumfassende Definition wird uns aktuell nicht gelingen, ist aber auch nicht notwendig.
Warum brauchen wir nun aber überhaupt Digitale Zwillinge?
Aus der Notwendigkeit von Daten und Auswertungen zur Effizienzverbesserung der Produktion könnte man die folgenden Schritte ableiten, um einen positiven Effekt zu erreichen:
- Zentralisieren von allen bisher schon anfallenden Daten
Alle bisher schon anfallenden Daten z.B. einer Maschine werden aktuell in den meisten Betrieben in eigenen Systemen je nach Aspekt abgespeichert. So liegen z.B. Daten über die Wartung in einer Excel Tabelle beim verantwortlichen Meister, die Daten der Qualitätskontrolle der Werkstücke aber in einer CAQ Datenbank. Beide Datenaspekte sind nicht logisch verknüpft, obwohl sie einen direkten oder indirekten Zusammenhang haben könnten. Ob der Zusammenhang wirklich besteht, ist nicht ohne weiteres prüfbar. Erst wenn die Daten zentral und logisch verknüpft abgespeichert werden, ist es möglich Zusammenhänge (mit Hilfe von Software) zu erkennen. Daraus könnte ein Mehrwert generiert werden. - Standardisierte Schnittstellen
Werden Daten nun zentral abgespeichert, ist es von Vorteil das diese über standardisierte Schnittstellen erreichbar sind. Ist das der Fall, lassen sich sehr einfach automatische Informationsflüsse programmieren. Der Schritt vom einfachen Modell hin zum cyberphysischen System ist damit einfacher zu bewältigen. Der damit entstehende digitale Zwilling einer Komponente oder einer Maschine ist eine Grundlage für weiter folgende Auswertungen. - Aufsetzen von Business Logik
Sind alle Grundlagen für automatisierte Datenauswertungen geschaffen, ist es nun einfacher möglich, Software zu nutzen, die hilft, bessere Entscheidungen zu treffen oder gänzlich allein zu entscheiden (Business Logik). Hier entsteht nun der angestrebte Mehrwert.
Während Schritt 1 und 2 keinen oder nur wenig merkbaren Mehrwert schaffen, sind sie Grundlage für den Schritt 3.
Obwohl ich immer dafür plädiere eine Änderung oder Verbesserung im Produktionsprozess stets Anwendungsfall getrieben durchzuführen, kommt man schnell zu der Erkenntnis, dass ein gewisser Basisaufwand notwendig sein wird. Die Erstellung von digitalen Zwillingen ist eine notwendige Basis für den zukünftigen Erfolg. Somit sind sie eine wichtige Säule im Kontext von Industrie 4.0.
Praktischer Lösungsweg
Um möglichst klein anfangen zu können, später aber darauf agil aufzubauen, eignet sich das Konzept der Asset Administration Shell der Plattform Industrie 4.0. In diesem Konzept sind allgemeingültige Schnittstellen vordefiniert. Anwendungsfall spezifische Schnittstellen können leicht nachgerüstet werden. Dieses Konzept bietet Grundlagen für die Erstellung eines standardisierten digitalen Zwillings einer jeden Komponente. Ob man nun dieses Konzept als Startpunkt wählt oder ein komplett eigenes Informationsmodell programmiert ist sicherlich Geschmackssache.
Verbreitete Standards haben aber die Vorteile, dass Daten interoperabel sein können, was vor allem in Kunden/Lieferanten Beziehungen sehr von Vorteil ist. Auch ist zu erwarten, dass es auf dem Markt wiederverwendbare Software geben wird, die eben genau mit diesen Standards umzugehen vermag. Die Industrietauglichkeit des Konzeptes Asset Administration Shell zur Erstellung von Digitalen Zwillingen ist in 2022 erreicht worden und verbessert sich zunehmend. Es wird nun Zeit komplexe Projekte damit umzusetzen.
Quellen:
[1] J. Hagerty: 2017 Planning Guide for Data and Analytics. Gartner 2016
[2] W. Kritzinger, M. Karner, G. Traar, J. Henjes und W. Sihn: 2018 Digital Twin in manufacturing: A categorical literature review and classification.
*Die originale Definition wählt das Wort Asset, anstatt Produkt. Ich verwende hier aber die vereinfachte Wortwahl, auch wenn das nicht vollumfänglich ist.
[…] Die Asset Administration Shell (AAS) ist ein aufstrebendes Konzept im Zusammenhang mit der Datenhaltung eines Digitalen Zwillings. Es handelt sich dabei um eine virtuelle Repräsentation einer physischen oder logischen Einheit, wie beispielsweise einer Maschine oder eines Produkts. Die AAS ermöglicht es, relevante Informationen über diese Einheit zu sammeln, zu verarbeiten und zu nutzen, um eine effiziente und intelligente Produktion zu gewährleisten. Die Architekturstandardisierung der AAS ermöglicht die Kommunikationen zwischen digitalen Systemen und ist damit die Grundlage für Cyber Physical Systems (CPS). Die Herleitung des Bedarfs eines Digitalen Zwillings in der Industrie finden Sie hier: ZEISS Digital Innovation Blog – Der digitale Zwilling als eine Säule von Industrie 4.0 […]
[…] The Asset Administration Shell (AAS) is an emerging concept in connection with the digital twin data management. It is a virtual representation of a physical or logical unit, such as a machine or a product. The AAS enables relevant information about this unit to be collected, processed and used to ensure efficient and intelligent production. The architectural standardization of the AAS enables communication between digital systems and is therefore the basis for Cyber Physical Systems (CPS). You can find out more about the need for digital twins in the industry here: ZEISS Digital Innovation Blog – The digital twin as a pillar of Industry 4.0 […]